Fertigungstechnologien für den 3-D-Druck in der Zahnheilkunde
Die Entwicklungsgeschwindigkeit im Bereich der digitalen dentalen Fertigungstechnologien hat ein enormes Tempo angenommen. Während im Bereich der subtraktiven Verfahren bereits ein hohes Produktivitätsniveau mit optimalen Passungen erreicht ist, gewinnen additive Verfahren (3-D-Druck) zunehmend an Bedeutung. Aber auch Kombinationen aus verschiedenen Fertigungsverfahren zeigen enormes Potenzial, so beispielsweise die Verknüpfung des Lasersinterns mit der CNC-Bearbeitung oder aber die Kombination von digitaler Konstruktion und 3-D-Druck mit dem analogen Fertigungsweg der Keramikpresstechnik [Schweiger et al., 2020; Schweiger und Güth, 2020].
Der große Vorteil aller additiven Verfahren liegt darin, dass dreidimensionale Objekte in nahezu uneingeschränkter Formvielfalt und Komplexität am Computer konstruiert und umgesetzt werden können. Ein bislang wenig beachteter Aspekt ist, dass während des Bauprozesses die mechanischen und die ästhetischen Eigenschaften des zu druckenden Bauteils beeinflusst werden können. Dies ist bei der subtraktiven Fertigung nicht möglich; hier sind die Werkstoffeigenschaften in der konfektionierten Ronde vom Hersteller definiert. Diese Individualisierung sowie die Möglichkeit, digital entworfene Produkte schneller und leichter verfügbar zu machen oder sogar kostengünstiger zu produzieren, machen die additive Fertigung zu einem Eckpfeiler in der digitalen Zahnheilkunde (Dentistry 4.0) [Caviezel et al., 2017; Kessler et al., 2020; Kieschnick et al., 2020].
Geschichte des 3-D-Drucks
Schon Anfang der 1980er-Jahre kamen erste industrielle Maschinen für die additive Fertigung (geläufiger Begriff: 3-D-Druck) auf den Markt. Als Pioniere des 3-D-Drucks sind Charles Hull (Gründer von 3-D-Systems), S. Scott Crump (Gründer von Stratasys) und Hans J. Langer sowie Hans Steinbichler (beide Gründer von EOS) zu nennen. Der erste 3-D-Drucker wurde 1986 von Charles Hull zum Patent angemeldet [Hull, 1984]. Zum damaligen Zeitpunkt wurden die Drucker hauptsächlich zur Herstellung von Prototypen eingesetzt (Rapid Prototyping). In den Folgejahren entwickelte sich die Technik rasant. Mit dem Auslaufen des Patents für das sogenannte FDM-Verfahren (FDM = Fused Deposition Modeling) im Jahr 2009 [Crump, 1989] traten die „3-D-Drucker“ ihren Siegeszug auch im Consumer-Bereich an. Letztendlich übertrug sich diese Dynamik verstärkt auch auf den Dentalbereich. Die Drucker wurden kleiner und günstiger. Die Einsatzgebiete veränderten sich. Die zu druckenden Materialien erweiterten sich auf Kunststoff, Metall, Keramik bis hin zu menschlichem Gewebe.
Nomenklatur und Einteilung der additiven Verfahren
Als additive Fertigungsverfahren (AM = Additive Manufacturing) bezeichnet man Herstellungsprozesse, bei denen auf der Grundlage dreidimensionaler Modelle schichtweise Bauteile hergestellt werden. Im allgemeinen Sprachgebrauch wird der Begriff „3-D-Druck“ als Synonym für alle additiven Verfahren angewandt [Kollenberg, 2014]. Nach der Terminologienorm DIN EN ISO/ASTM 52900 handelt es sich bei einem AM-Verfahren um einen „Prozess, der durch Verbinden von Material Bauteile aus 3-D-Modelldaten, im Gegensatz zu subtraktiven und umformenden Fertigungsmethoden, üblicherweise Schicht für Schicht, herstellt“ [Beuth, 2024]. In der DIN EN ISO 17296-2 werden die Prozessgrundlagen der additiven Fertigung beschrieben. Dabei wird auch eine Übersicht über die bestehenden Prozesskategorien gegeben, die jedoch aufgrund der dynamischen Entwicklung neuer Technologien nicht umfassender Natur sein kann.
Folgende sieben Prozesskategorien (Abbildung 1) können in der additiven Fertigung unterschieden werden [Beuth, 2024]:
Photopolymerisation im Bad (Vat photopolymerization = VPP)
Materialextrusion (Material extrusion = MEX)
Freistrahl-Materialauftrag (Material jetting = MJT)
Freistrahl-Bindemittelauftrag (Binder jetting = BJT)
Pulverbett-basiertes Schmelzen (Powder bed fusion = PBF)
Materialauftrag mit gerichteter Energieeinbringung (Directed energy deposition = DED)
Schichtlaminierung (Sheet lamination = SHL)
Additive Fertigung im Dentalbereich
Die additiven Fertigungsverfahren sind im Dentalbereich schon seit längerer Zeit etabliert. Prominentes Beispiel ist das Lasersinterverfahren der Firma Bego Medical (Bremen, D) [Dolabdjian und Strietzel, 2000]. Die Vorstellung der Technologie sorgte im November 2002 für großes Aufsehen. Fachleute bescheinigten dieser Verfahrenstechnik bereits damals ein hohes Potenzial.
Die Grundlage für den additiven Aufbau der Materialien sind STL-Dateien. Dabei wird die Oberfläche eines Objekts durch kleine Dreiecke beschrieben (Abbildung 2). Grundsätzlich führt die Annäherung an die exakte Kontur durch Dreiecke zwar zu relativen Ungenauigkeiten. Diese werden jedoch umso geringer, je größer die Anzahl der Dreiecke und somit je kleiner deren Größe ist (= Sekantenfehler) (Abbildung 3). Um das STL-Format im jeweiligen additiven Verfahren verarbeiten zu können, müssen die Daten mathematisch in Z-Richtung (3. Dimension) in einzelne Schichten zerlegt werden („Slicen“). Anhand der „geslicten“ Daten können die einzelnen Schichten nun additiv aufeinandergelegt werden [Schweiger und Kieschnick, 2023].
Verfahrensablauf des 3-D-Drucks
Alle additiven Technologien gleichen sich im Verfahrensablauf, der in vier Bereiche gegliedert werden kann. Folgende Schritte werden unterschieden:
Generieren des 3-D-Datensatzes
Das Generieren des 3-D-Datensatzes kann zum Beispiel durch einen Scanner oder eine CAD-Konstruktion erfolgen.
Zerlegen des CAD-Datensatzes („Slicen“)
Der STL-Datensatz wird von einer speziellen Software „Slicer-Software“ (zum Beispiel 3Shape CAMbridge, BEGO CAMCreator, Formlabs PreForm, Netfab von Autodesk, Chitubox von CDB-Tech) in einzelne Schichten zerlegt (Abbildung 4).
Schichtweises Aufbauen des Bauteils auf Basis der „geslicten“ Daten
Im additiven Verfahren wird das Bauteil auf Basis der geslicten Daten schichtweise aufgebaut, wobei die Genauigkeit in Baurichtung (Z-Richtung) wesentlich von der Schichtdicke abhängt. Die einzelnen Schichten sind im späteren Bauteil immer sichtbar. Selbst bei sehr hoher Auflösung, also minimaler Schichtdicke und höchster Präzision der Umrisse, bleiben sie erkennbar und verleihen den Bauteilen eine mehr oder minder raue Oberfläche, die gegebenenfalls nachbearbeitet werden kann. Man nennt diesen Effekt auch Z-Stufung beziehungsweise XY-Stufung (Abbildungen 5 und 6).
Manuelle Nachbearbeitung des Objekts
Die manuelle Nachbearbeitung kann je nach Aufbauverfahren verschiedene Arbeitsschritte erfordern (Abbildung 7). Unter anderem können folgende zusätzliche Arbeitsgänge erforderlich sein:
Reinigung
Entfernen und Verschleifen der Stütz- beziehungsweise Supportstrukturen
Entgraten
Nachpolymerisation = Post-Curing (optional)
Politur beziehungsweise Lackierung
3-D-Druck-Verfahren für die Anwendung im Dentalbereich
Im Folgenden werden die für die Anwendung in der digitalen Zahnheilkunde geeigneten Technologien vorgestellt und jeweils Anwendungsbeispiele dafür gezeigt.
Stereolithografie (SLA)
Die Stereolithografie ist die älteste Verfahrenstechnik in der additiven Fertigung und wurde im Jahr 1986 von Charles Hull, dem Gründer von 3-D-Systems, zum Patent angemeldet. Die SLA-Technologie beruht auf der punktweisen Verfestigung eines Harzbades mittels Laserstrahl (Abbildung 8) [Revilla-León und Öczan, 2020; Jokusch und Öczan, 2020; Quan et al., 2020]. Beispiele für SLA-Drucker sind die 3-D-Drucker von Formlabs (Form 2, Form 3B+, Form 3BL) (Formlabs, Somerville, MA). Das SLA-Verfahren zeichnet sich durch seine hohe Präzision aus.
Maskenbelichtungsverfahren (Digital Light Processing DLP) mit DLP-Projektor oder LCD-Display
Das Maskenbelichtungsverfahren funktioniert ähnlich wie die Stereolithografie. Als Lichtquelle wird jedoch anstelle eines Lasers ein DLP-Projektor oder ein LCD-Display verwendet. So kommen beispielsweise Blaulicht-LEDs zum Einsatz.
Aufgrund der hohen Baueffizienz sind 3-D-Drucker auf Basis des Maskenbelichtungsverfahrens inzwischen sehr weit verbreitet. Da die Bauplattform in einem Belichtungsschritt spezifisch ausgehärtet werden kann, ist das Maskenbelichtungsverfahren um ein Vielfaches schneller als die klassische SLA-Technologie, bei der der Laserstrahl in einzelnen „Fahrspuren“ das Bauteil je Schicht aushärtet. Maskenbelichtungs- und SLA-Technolgie haben sowohl Vor- als auch Nachteile. Beide unterscheiden sich insbesondere durch folgende Eigenschaften:
DLP-Verfahren zeigen sowohl eine Z- als auch eine XY-Stufung (Abbildung 11).
SLA-Verfahren haben nur eine Z-Stufung (Abbildung 12).
DLP-Verfahren sind in der Baugeschwindigkeit schneller.
SLA-Verfahren liefern sehr schöne Oberflächen.
DLP-Verfahren werden im Dentalbereich beispielsweise auch für den 3-D-Druck von definitiven Komposit-Restaurationen verwendet. Seit Februar 2020 bietet BEGO weltweit erstmals die Möglichkeit, Einzelzahnversorgungen mittels 3-D-Druck aus einem keramisch gefüllten Hybridmaterial herzustellen. Mit der BEGO VarseoSmile Crown plus können Einzelzahnkronen, Inlays, Onlays und Veneers im additiven Verfahren hergestellt werden (Abbildungen 13 bis 16). In wissenschaftlichen Studien wurde das Material umfangreich untersucht und zeigte dabei hervorragende Ergebnisse [Schweiger et al., 2021; Graf et al., 2022].
Lasersinter-Verfahren (LPBF, LS, SLS, DMLS, SLM)
Im Gegensatz zum SLA-Verfahren werden beim Lasersintern keine flüssigen Werkstoffe verfestigt. Das Lasersintern erfolgt auf Basis von Pulvern. Die einzelnen Pulverkörnchen werden mit einem Laserstrahl an- oder aufgeschmolzen. Ähnlich wie beim SLA beruht dieses Verfahren jedoch auf einem schichtweisen Aufbau des Bauobjekts in die Z-Richtung. Die Pulverschichten werden mit einer Glättungswalze oder einem Wischer schichtweise über die Bauplattform gezogen und anschließend durch den Laserstrahl verschmolzen. Danach senkt sich die Bauplattform in Z-Richtung ab. Das Wischersystem trägt die nächste Pulverschicht auf. Als Laserstrahlquelle kommen – je nach Anwendung – CO2-Laser mit einer Leistung von 50 Watt beim Kunststoffsintern und bis zu 250 Watt beim Sintern von reinen Metallpulvern zum Einsatz.
Inzwischen hat sich das Lasersintern als ein Standardverfahren zur Herstellung von CoCr-Einheiten für die Kronen- und Brückentechnik etabliert [Revilla-León et al., 2019]. Durch Optimierung des Postprozessing nach dem eigentlichen Bauvorgang ist es mittlerweile möglich, absolut spannungsfreie und passgenaue NEM-Gerüste auch über größere Spannweiten herzustellen. Aufgrund der großen Anzahl von Einheiten, die auf einer Bauplattform positioniert werden können (Abbildung 17), reduziert sich die Fertigungszeit je Einheit auf wenige Minuten. Das Verfahren ist damit extrem kostengünstig und es hat sich daher im Bereich der Versorgung mit festsitzenden NEM-Restaurationen etabliert. Die physikalischen und mechanischen Eigenschaften von lasergesinterten Kronen- und Brückengerüsten aus NEM sind vergleichbar mit gegossenen Restaurationen [Fischer et al., 2008; Rudolph und Setz, 2007].
Auch für die Herstellung von klammerretiniertem Zahnersatz aus CoCr-Legierungen (Klammermodellguss-Prothesen) hat sich seit dem Jahr 2020 das direkte Lasersintern als das Standardverfahren im Bereich der digitalen Zahnheilkunde etabliert (Abbildungen 18 und 19). Aktuelle Publikationen sehen in der digitalen Fertigung mittels Lasersinter-Verfahren Vorteile in der Standardisierung, in der verringerten Produktionszeit und im einfachen Transfer von digitalen Daten sowie in der hohen Wirtschaftlichkeit. In einer In-vitro-Untersuchung wurde an der Poliklinik für Zahnärztliche Prothetik der LMU München die „mechanische Qualität gegossener versus lasergesinterter Klammern für Modellgussprothesen“ untersucht [Schweiger et al., 2019]. Die Ergebnisse der Studie zeigten das hohe mechanische Potenzial von lasergesintertem klammerretinierten Zahnersatz aus CoCr-Legierungen.
Extrusionsverfahren = Fused Filament Fabrication (FFF), Fused Deposition Modeling (FDM)
Beim FFF-Verfahren wird ein Bauteil schichtweise mit schmelzbarem Kunststoff aufgebaut. Der als Draht vorliegende, thermoplastische Kunststoff wird erhitzt, durch eine feine Düse gepresst und Schicht für Schicht aufgetragen (Abbildung 19). Das Verfahren wurde vom Stratasys-Gründer S. Scott Crump in den späten 1980er-Jahren entwickelt [Crump, 1989]. Grundsätzlich ist dieses Verfahren für alle thermoplastischen Kunststoffe geeignet, was gerade bei der Zulassung von Werkstoffen für die dentale FDM-Anwendung einen großen Vorteil bietet, da auf bereits zugelassene Werkstoffe zurückgegriffen werden kann.
Das folgende Beispiel zeigt den Einsatz der FFF –Technologie im Dentalbereich: Der FilaPrintM Dental Desktop 3-D-Drucker ist ein Gemeinschaftsprojekt von Heimerle + Meule GmbH, (Pforzheim, D) und DentalPlus GmbH (Samerberg, D). Der Drucker ist insbesondere auf die Anwendung im Dentalbereich optimiert. Ein besonderes Merkmal des FilaPrint M ist der „Drive Belt“, eine Bauplattform in Fließbandform, mit der fortlaufend produziert werden kann, da die Bauteile automatisch durch das Bewegen des „Drive Belt“ von der Bauplattform abgelöst werden. Damit ist ein Betrieb im 24/7-Modus ohne Unterbrechung möglich.
Freier Materialauftrag (MJT, MJM, MJF, MJP, Polyjet) = direkter 3-D-Druck (3-DP)
Auch der eigentliche 3-D-Druck (3 DP) wird im Dentalbereich schon seit längerer Zeit von diversen Herstellern angeboten. Grundsätzlich können vier Fertigungsvarianten des direkten 3-D-Drucks unterschieden werden:
Wachs drucken
Pulverbett drucken
Kunststoff drucken
Multimaterial-3-D-Druck
Das direkte 3-D-Kunststoffdrucken und der Multimaterial-3-D-Druck werden aktuell verstärkt im Dentalbereich eingesetzt. Insbesondere sind hier das PolyJet-Verfahren (Stratasys, Eden Prairie, MN) und das Multi-Jet-Printing (3-D Systems, Rock Hill, SC) zu nennen. Die Polyjet-Technologie ist durch einen extrem schnellen Bauprozess und eine hohe Präzision gekennzeichnet [Dietrich et al., 2017; Brown et al., 2018; Kim et al., 2018].
Multimaterial-3-D-Druck – eine Anwendung mit extrem großem Zukunftspotenzial
Die digitale dentale Multimaterial-Fertigung beruht auf dem Prinzip, dass bereits bei der CAD-Konstruktion einem Bauteil, zum Beispiel einem Meistermodell oder Zahnersatz, verschiedene räumlich definierte Eigenschaften zugeordnet werden. Dies können beispielsweise Farbinformationen oder materialspezifische Charakterisierungen sein. Die Grundlage für die Multimaterial-Fertigung kann bereits im Mund mit der digitalen Erfassung durch einen 3-D-Intraoralscanner gelegt werden. Dabei werden seit einigen Jahren zusätzlich zu den dreidimensionalen Oberflächendaten auch die geometriebezogenen Farbinformationen aufgezeichnet. Spezielle Dateiformate, wie beispielsweise das DCM-Format, das PLY-Format, das OBJ-Format oder das 3MF-Format, ermöglichen die Speicherung von Farbinformation in Relation zu den Oberflächendaten. Das heißt, jedem Oberflächenpunkt wird eine spezifische Farbe zugeordnet. Und diesen Mehrwert an Information kann man bei der Herstellung von Meistermodellen und Zahnersatz nutzen. Die digitale dentale Multimaterial-Fertigung ist sowohl mittels abtragender Verfahren (= subtraktive Verfahren = CNC-Fräsen) als auch mittels additiver Verfahren (= 3-D-Druck) umsetzbar. Insbesondere der 3-D-Druck bietet hier zukünftig ungeahnte Entwicklungsmöglichkeiten, die die Fertigung sowohl von Kunststoffen, von Keramiken als auch von Metallen betreffen.
Multimaterial-3-D-Druck von Kunststoff
Die für den dentalen Multimaterial-3-D-Druck derzeit relevanteste Technologie ist das Material-Jetting, bei dem in das in spezieller Flüssigkeit beigemischte Material – ähnlich wie beim Tintenstrahldruck – über Druckdüsen auf eine Bauplattform aufgesprüht wird, dort schnelltrocknet und sich verfestigt. Drucker mit dieser Technologie werden von verschiedenen Unternehmen angeboten, beispielsweise von Stratasys (Eden Prairie, MN). Hersteller, die Multimaterial-Fertigung im Kunststoffbereich anbieten, sind Mimaki (Nagano, JP), 3-D-Systems (Rock Hill, SC, USA), Quantica (Berlin) sowie Hewlett Packard (Palo Alto, CA, USA). Aktuell werden die Technologien von HP jedoch nicht für den Dentalbereich angeboten.
Auf der Basis von intraoralen 3-D-Farbscans können mithilfe des Multimaterial-3-D-Drucks farbige Meistermodelle hergestellt werden, die die Mundsituation in realistischen Farben wiedergeben. Aktuell gibt es drei verschiedene 3-D-Drucktechnologien, die die Herstellung von grafischen 3-D-Modellen ermöglichen. Die erste dazu geeignete Technik war das sogenannte Pulverbett-Druckverfahren (Binder-Jetting), bei dem unterschiedlich eingefärbte Binderflüssigkeiten in ein Pulverbett gespritzt werden und so einerseits das Bauteil verfestigt und andererseits die Farbe des gedruckten Objekts definiert wird. Diese Technologie findet im Dentalbereich keine Anwendung. Mit der Einführung des Multimaterial-3-D-Drucks im Material-Jetting-Verfahren ergaben sich ganz neue Möglichkeiten bei der Anfertigung von dentalen Bauteilen [Schweiger et al., 2014; 2015; 2019]. Im Dentalbereich findet das Material-Jetting-Verfahren derzeit bei der Herstellung von grafischen 3-D-Modellen und Totalprothesen Anwendung (Abbildungen 23 und 24) [Schweiger et al., 2022; 2023].
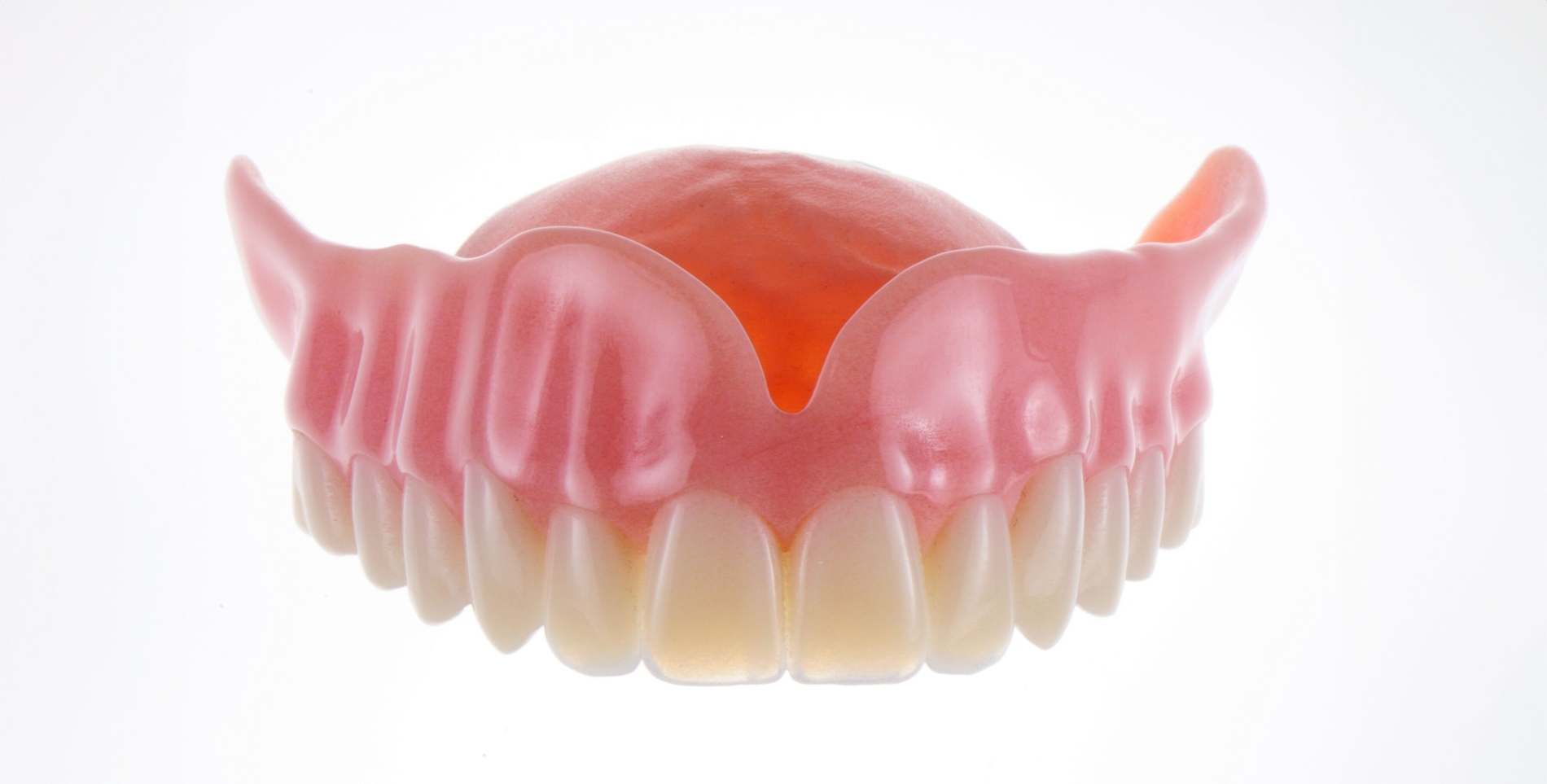
Multimaterial-3-D-Druck von Keramik
Mithilfe des Multimaterial-3-D-Drucks ist man in der Lage, mehrschichtige Vollkeramikkronen (beispielsweise aus Lithiumdisilikat) additiv in einer natürlichen 3-D-Schichtung herzustellen. Der 3-D-Drucker-Hersteller Lithoz (Wien, A) hat in einer ersten Machbarkeitsstudie gezeigt, dass es mit der patentierten LCM-Technologie (LCM = Lithography-based Ceramic Manufacturing) möglich ist, Zähne aus Lithiumdisilikat in einer natürlichen Dentin-Schneide-Schichtung zu drucken (Abbildungen 25 und 26). Die ersten Ergebnisse sind beeindruckend und lassen auf das disruptive Potenzial dieser Technologie schließen [Schweiger et al., 2024].
Der Multimaterial-3-D-Druck von geschichteten Vollkeramikrestaurationen aus Lithiumdisilikat ermöglicht die exakte dreidimensionale Kopie natürlicher Zähne. Zahnstrukturdatenbanken (zum Beispiel ExoCAD Cutback libraries) sowie die digitale intraorale Erfassung der dreidimensionalen Zahnschichtung mittels NIRI-Technologie werden zukünftig die Datengrundlage für diese Technologie bilden. Da für mehrschichtig gedruckte Keramikrestaurationen keinerlei manuelle Schichtung erforderlich ist, sollte die Stabilität und Zuverlässigkeit derartiger Versorgungen wesentlich besser sein als bei den bisherigen analogen Schichttechniken. Wissenschaftliche Studien sind dabei ein wesentlicher Aspekt bei der Entwicklung und Markteinführung dieser Technologie.
Multimaterial-3-D-Druck von Metall
Auch im Bereich der Metallfertigung gibt es Bestrebungen zur Herstellung von Bauteilen aus verschiedenen Metallen in einem einzigen Bauprozess. Als Vorreiter ist hier das Fraunhofer IGCV in Augsburg zu nennen, das sich seit einigen Jahren mit dem Metall-Multimaterial-3-D-Druck beschäftigt und erste Arbeitsansätze im Dentalbereich vorgestellt hat [Horn et al., 2023].
Ein aktuelles Forschungsprojekt in Zusammenarbeit mit der Poliklinik für Zahnärztliche Prothetik der LMU München befasst sich mit der Entwicklung einer innovativen Fertigungstechnologie zur Produktion von Doppelkronen-Prothesen aus Edelmetall in Kombination mit einer CoCr-Legierung (Abbildungen 27 bis 29). Der wesentliche Vorteil liegt hierbei darin, dass es mithilfe desMultimaterial-3-D-Drucks möglich ist, mit verschiedenen Metallenin einem Bauprozess unterschiedliche Eigenschaftenzu kombinieren und dabeidas Bauteil in einem einzigen 3-D-Druckvorgang herzustellen.So kann man beispielsweise die hohe Stabilität von CoCr-Gerüsten mit den hervorragenden Friktionseigenschaftenvon Gold in einer Multimaterial-Teleskoparbeitkombinieren. Da hierbei keine zusätzlichen Fügeschritte (Löten, Lasern, Kleben)notwendig sind, ergibt sich daraus eine sehrkosteneffiziente Herstellungsvariante.
Ausblick
Additive Verfahren haben den wesentlichen Vorteil, dass die Eigenschaften der Bauteile während des Bauprozesses individuell beeinflusst werden können. Dies betrifft sowohl die mechanischen als auch die ästhetischen Eigenschaften. Bei subtraktiven Verfahren hingegen sind diese Charakteristika bereits mit der Herstellung des Fräsrohlings determiniert. Damit eröffnet der 3-D-Druck enorme Freiheiten schon beim Design-Prozess. Andererseits sind die Präzision und die Effizienz der subtraktiven Bearbeitung extrem hoch, so dass die Kombination aus beiden Fertigungstechniken im Sinne einer Hybridfertigung äußerst sinnvoll erscheint.
Mit einer sehr hohen Wahrscheinlichkeit werden diejenigen Fertigungstechnologien „das Rennen machen“, die es ermöglichen, direkt aus dem Konstruktionsdatensatz die finale Restauration herzustellen – ohne analoge Zwischenschritte, die letztlich aufgrund der menschlichen Arbeitszeit und des zusätzlichen Material- und Energieaufwands das Produkt verteuern, wodurch jenes mittelfristig nicht konkurrenzfähig sein wird.
Schlussbetrachtung
Additive Fertigungsverfahren sind inzwischen in der Zahnheilkunde angekommen. Der Einsatz der Technologien ist sehr vielseitig und das Anwendungsspektrum reicht beispielsweise von der digitalen Herstellung von Meistermodellen, Bohrschablonen und individuellen Löffeln bis hin zur Fertigung von definitiven Restaurationen und Totalprothesen. Der 3-D-Druck erfordert eine hohe Anwenderkompetenz, die durch Schulungen und letztlich auch durch die praktische Arbeit erreicht werden kann. Vorteilhaft sind hier sicherlich Systeme, die den Workflow vollumfänglich abbilden, also sowohl die digitale Vorbereitung (Nesten, Slicen) der Datensätze ermöglichen als auch das Postprocessing (Säubern und Nachvergüten) in einem geschlossenen System anbieten. Dies führt nicht nur zu einer höheren Anwendungssicherheit, sondern verringert auch das Gefahrenpotenzial durch unsachgemäßen Umfang vor allem beim Postprocessing.
Einen sehr interessanten Ansatz bietet die sogenannte „Chairside by Lab“-Lösung. Dabei werden Intraoral-Scandaten aus der zahnärztlichen Praxis ins zahntechnische Labor gesendet, wo die CAD-Konstruktion des zu druckenden Bauteils erfolgt. Anschließend werden die Konstruktionsdaten online an den 3-D-Drucker in der zahnärztlichen Praxis gesendet, wo die additive Fertigung der Bauteile erfolgt. Die Finalisierung (Postprocessing) der Bauteile erfolgt in der Praxis. Der Vorteil hierbei ist, dass einerseits auf die fachliche Kompetenz im zahntechnischen Labor zurückgegriffen werden kann, andererseits kein Versand der Produkte notwendig ist. Dies erspart Zeit und schont Ressourcen, da kein physischer Versand notwendig ist.
Literaturliste
Brown GB, Currier GF, Kadioglu O, Kierl JP. Accuracy of 3-dimensional printed dental models reconstructed from digital intraoral impression. Am J Orthod Dentofacial Orthop. 2018; 154(5):733-739.
Campbell SD, Cooper L, Craddock H, hyde TP, Nattress B, Pavitt SH, Seymour DW: Removable partial dentures: The clinical need for innovation. J Prosthet Dent. 2017; 118(3):273-280.
Caviezel C, Grünwald R, Ehrenberg-Silies S, Kind S, Jetzke T, Bovenschulte M. Additive Fertigungsverfahren (3-D-Druck) – Innovationsanalyse. Büro für Technikfolgen Abschätzung beim Deutschen Bundestag 2017; Arbeitsbericht Nr. 175.
Charles W. Hull: Apparatus for Production of Three-Dimensional Objects by Stereolithography. U.S. Patent 4,575,330 (1984).
Crump S: Apparatus and Method for Creating Three-Dimensional Objects. U.S. Patent 5,121,329 (1989).
Dawood A, Marti B, Sauret Jackson V, Darwood A. 3-D printing in dentistry. Br Dent J 2015; 219(11):521-529.
Dietrich CA, Ender A, Baumgartner S, Mehl A. A validation study of reconstructes rapid prototyping models produces by two technologies. Angle Orthod. 2017; 87(5):782-787.
DIN EN ISO 17296-2:2016-12: dx.doi.org/10.31030/2580024 (Zugriff am 05.04.2024).
DIN EN ISO/ASTM 52900:2017-06: dx.doi.org/10.31030/2631641 (Zugriff am 05.04.2024).
Dolabdjian H, Strietzel R: Verfahren zur Herstellung von Zahnersatz und dentalen Hilfsteilen. EP 1 021 997 B2 (2000).
Douglass CW, Watson AJ. Future needs for fixed and removable partial dentures in the United States. J Prosthet Dent 2002;87:9–14.
Fischer J, Stawarczyk B, Trottmann A, Hämmerle CHF. Festigkeit lasergesinterter Brückengerüste aus einer CoCr-legierung. Quintessenz Zahntechnik 2008; 34(2):140-149.
Graf T, Erdelt KJ, Güth JF, Edelhoff D, Schubert O, Schweiger J. Influence of Pretreatment and Artificial Aging on the Retention of 3D-Printed Permanent Composite Crowns. Biomedcines 2022;10(9):2186 doi.org/10.3390/biomedicines10092186.
Horn M, Schweiger J, Schröder T, Langer L, Trimpl J, Erdelt K, Schubert O, Seidel C. Additive Multimaterialfertigung von Metallen in der Doppelkronentechnik. Quintessenz Zahntechnik 2023; 49(9):808-817.
Horn TJ, Harryson OLA. Overview of current additive manufacturing technologies and selected applications. Sci Prog 2012; 95(3):255-282.
Jokusch J, Öczan M. Additive manufacturing of dental polymers: An overview on processes, materials and applications. Dent Mater J. 2020;39(3):345-354.
Jordan RA, Micheelis W. Fünfte Deutsche Mundgesundheitsstudie (DMS V). Köln: Deutscher Zahnärzte Verlag 2016:18.
Kessler A, Hickel R, Reymus M. 3-D Printing in Dentistry – State of the Art. Oper Dent (2020);45(1):30-40.
Kieschnick A, Schweiger J, Edelhoff D, Güth JF. Status Präsens 2020: Additive CAD/CAM-gestützte Fertigungstechnologien im zahntechnischen Labor. Verband Deutscher Zahntechniker Innungen VDZI Sachverständigenpapier März 2020:1-16.
Kim SY, Shin YS, Jund HD, Hwang CJ, Baik HS, Cha JY. Precision and trueness of dental models manufactured with different 3-dimensional printing technologies. Am J Orthod Dentofacial Orthop. 2018; 153(1):144-153.
Kollenberg W: Keramik und Multimaterial 3D-Druck. Keram. Z. 2014; 66(4): 233-236.
Quan H, Zhang T, Xu H, Luo S, Nie J, Zhu X. Photo-curing 3D-Printing technique and its challenges. Bioact Mater. 2020; 22; 5(1):110-115.
Revilla-León M, Meyer MJ, Özcan M. Metal additive manufacturing technologies. Int J Comput Dent. 2019; 22(1):55-67.
Revilla-León M, Öczan M. Additive manufacturing Technologies Used for Processing Polymers: Current Status and Potential Application in Prosthetic Dentistry. J Prosthodont. 2019;28(2):146-158.
Rudolph M, Setz J: Ein CAD/CAM-System mit aufbauender Lasertechnologie. Quintessenz Zahntechnik 2007; 33(5):582-587.
Schweiger J, Trimpl J, Schwerin C, Güth JF, Edelhoff D: Biomaterials Update - Additive Manufacturing: Applications in Dentistry based on Materials Selection. Quintessence Dental Technician QDT 2019 (42):50-69.
Schweiger J, Güth J-F, Edelhoff D, Seidel K, Graf T. Application of 3D-printed colored 3D-models for the fabrication of full ceramic restorations: A technical report. J Esthet Restor Dent. 2022; 34(1):235-243.
Schweiger J, Edelhoff D, Schubert O. 3D-Printing of Lithium Disilicate Ceramics: Fact, Fiction, or Future? Quintessence Dental Technician QDT 2024 (47):178-189.
Schweiger J, Edelhoff D, Schubert O. CAD/CAM, 3D-Druck – und was kommt als nächstes? Bayerisches Zahnärzte Blatt BZB 2023; 60(12):52-57.
Schweiger J, Edelhoff D, Stimmelmayr M, Güth JF, Beuer F. Automated Production of Multilayer Anterior Restorations with Digitally Produced Dentin Cores. Quintessence Dental Technician QDT 2015 (38);207-220.
Schweiger J, Edelhoff D, Stimmelmayr M, Güth JF, Beuer F. Automatisierte Fertigung von mehrschichtigem Frontzahnersatz mithilfe digitaler Dentinkerne. Quintessenz Zahntechnik 2014; 40 (10): 1248-1266.
Schweiger J, Güth JF, Erdelt KJ, Edelhoff D, Schubert O: Internal porosities, retentive force, and survival of cobalt-chromium alloy clasps fabricated by selective laser sintering. J Prosthodont Res 2019; 64(2):210–216.
Schweiger J, Erdelt KJ, Edelhoff D, Müller H, Güth JF. 3-D-Druck von definitivem Zahnersatz - Dezementierungsverhalten und Bruchfestigkeit von Kronen aus VarseoSmile Crownplus von BEGO. Quintessenz Zahntechnik 2021; 47(4): 374-381.
Schweiger J, Kieschnick A: 3D-Druck & CAD/CAM in der digitalen Zahnheilkunde.Teamwork Media 2023.
Schweiger J, Edelhoff D, Güth JF. Update digitale Zahnheilkunde 2020 – aktuelle Möglichkeiten und Limitationen. Bayerisches Zahnärzte Blatt BZB 2020; 57(10):42-52.
Schweiger J, Güth JF. Neue Entwicklungen in der additiven und subtraktiven Fertigung Teamwork J CONT DENT EDUC 2020; 23(2):82-90.
Van Noort R. The future of dental devices is digital. Dent Mater 2012; 28(1):3-12.